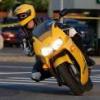
Run down to the basement. Using the dremel, with a wire wheel attachment, get the final paper out of the old air filter housing.
A blast of compressed air blows all the fibers out and away. Using a small drill bit, I put a couple of holes in the housing. I put the UNI foam (two layers of the HF series) into the housing and safety wired them in.
(Note: I thought I had the picture of that with me... where did that go?)
I put the air filter into the air box, but didn't screw down the top.
25 April 2009, 0530 hrs
Yes, another early Saturday morning. My wife had split for work at 4 am, but I just couldn't get up. My 2 YO daughter (the wrench-ess) had decided my bed was the place to be. So, up and at'em! Down a bowl of shredded wheat, grabbed my sippy cup (insulated coffee mug with a flip top, a sippy cup for adults) and headed to the basement.
I started putting the forks back together. I don't have a fork seal tool, so I had to improvise. At Trace's suggestion, I started looking for the bizillion PVC fittings I normally have laying around. None were to be found this morning. The story of my life, I know I have stuff, just do not know where it is.
So, I cut a slot into a 1.5" ID Schedule 40 PVC in my chop saw. About, say 6" long. I then turned it sideways (the way you're supposed to cut on a chop saw) and cut my seal press.
This 'halved' PVC pipe fit right over the fork tube.
P4250001.JPG
So, new slider bushing on, fork oil seal on, slide the tube in. Slide the seal down. Using the two pieces of PVC (deburred and cleaned mind you!), I alternately whacked each side with a rubber mallet. Note to self: next time use more oil on the seal.
Seal in, now for the dust seal. Easy squeezy.
I had previously cleaned out the damping rods, in it went. New copper washer and the damping rod bolt went in easily. Torqued without spinning (I've read the horror stories).
Now it's time to fill with the new PJ-1 oil. Manual says 15.5 ounces. In it goes. Slide the fork tube (at least 5 times per SM). And then the damping rod. It was quite easy at first, until it started to fill up. WOW.
Check the level. What a PITA. Next time I'm buying a turkey baster. Ugh.
Now for the new goodies. I open the Sonic Springs package. I clean the old springs. HUGE difference in length. Their instructions say that most modern sportbikes will use the stock spacer. Apparently the 2000 VFR is not modern enough.
P4250002.JPG
Ok. So, I know I now have a heavier rate, and probably won't need as much preload, but I decided to make the spacer 5MM longer. I'll back the preload out and adjust from there. (My previous setting was all the way in, most preload, with the stock springs).
P4250004.JPG
The tubes go back together with out a hitch and I put the forks into the triple trees. I get everything torqued down and buttoned up (not at easy as I just typed, darn delay valve is a pain to work with) and look into my egg carton. Hmmm. Two retaining clips left over and my muffler clamp. Muffler clamp ok (muffler still on the shelf), but these two retaining wires.
OH, the clip ons! I put the forks in per manual 39MM above the triple. Sorry, not so much. It needs about 41MM so you can put the retaining wires back on. Crap. Loosen the pinch bolts. Rock the front end and voila! Torque everything back down.
By this time I've run back and forth / up and down the stairs to feed the kids, get them dressed and kick them out the door, it's already 60F outside, go play!
25 April 2009 2130hrs
The final throws of labor. I put the MIG back on, had to find a new bolt for the clamp. Luckily I had some cap head screws left over from the mirror extender builds. Worked like a charm, except I needed to rotate the clamp so the center stand wouldn't catch. Battery back in, BT leads connected, fuse box wired back in. All the tupperware back on. It's now 2330hrs.
Ok, screw it, take it off the table! It comes down with out much of a hitch, kick stand down, ready for tomorrow.
26 April 2009 0725hrs
Check tire pressure. Wheel the '00 to the french doors and into the back 'yard' (it's still fill and no grass)
P4260008.JPG
I turn the key and thumb the starter. The first time in over 6 months. JOY!!!!
I ride it to the garage, hit the 50 Cal button I installed and up the garage door went! WOOHOO!
Here's the maintenance tally:
Muffler: repacked and resprayed
Clutch fluid replaced.
Brake fluid replaced.
Motor oil and filter replaced.
Valves checked - within spec.
50 cal mounted (left garage bay door)
rocket launcher mounted (right garage bay door)
Fork oil and seals replaced
Fork spring replaced with Sonic Springs .90
Stock shock replaced with '00 929 shock
RedNeck Table built
'08 Ninja 250 purchased
Rode her in to work today. The sag on the front is about perfect. Sag on the rear needs to be checked.
She felt more planted then she has in a long time. 24k miles is a long time to go without doing a lot of the above.
By the way, the front brakes are really responsive, but the rear has a lot more throw than it used to. Of course with all the crud built up that is now gone, I'm not surprised.
I'm going to need a chain and a battery by the middle of the season. I'm sure the CFO will love to hear that.
I officially call this maintenance session complete!
:fing02:
- Read more...
- 3 comments
- 1,839 views